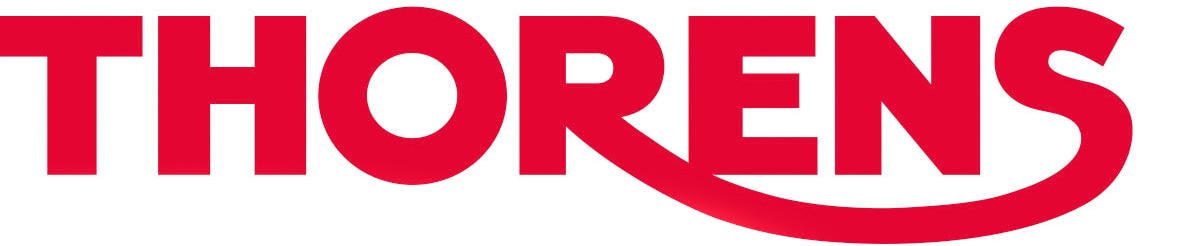
TD124 Main Spindle Bearing Rebuild
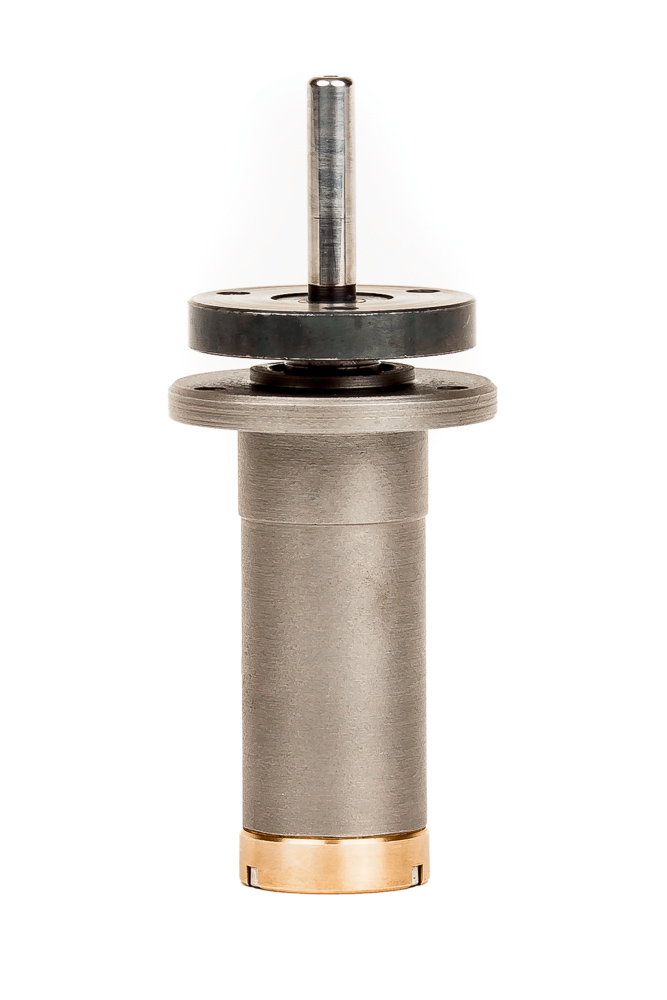
The main bearing is one of the most critical parts on a turntable. How the main bearing operates directly affects the audible playback qualities and unique sonic ‘signature’ of any turntable. Ideally, a turntable bearing will have a close tolerance fit between the spindle and the bearing liners, and it will operate in fully hydro-dynamic conditions, meaning that there is no contact between the bearing spindle and the bearing liners so that the spindle glides on a thin film of oil. However, in the real world, the majority of TD124 bearing rebuilds fall far short of this. Rebuilding a TD124 bearing is far more than pressing out the old bushings and pressing in new ones, yet, what is most commonly offered is nothing more than that.
We are offering what we believe to be the best rebuild service available for your Thorens TD124 main platter bearing.
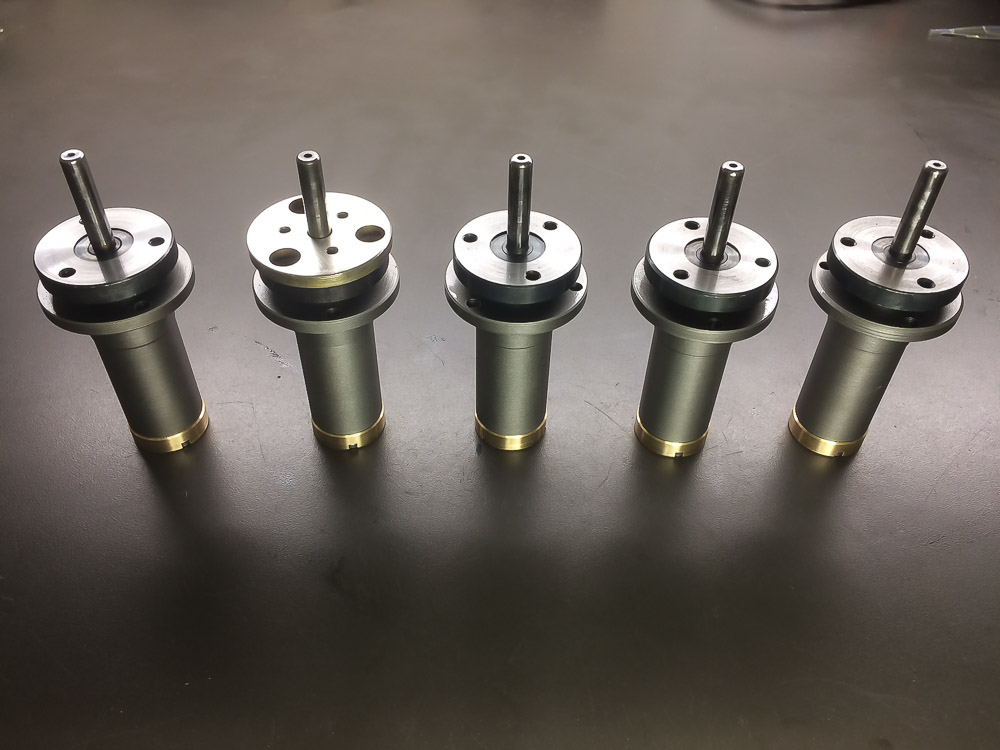
Achieving close tolerances between the spindle and bushings, and at the same time maintaining hydrodynamic operation, will reduce Wow & Flutter, improve speed stability, and lower noise, giving cleaner bass, greater dynamics, and improved sound stage. While these words are great, they are not easy to accomplish, and are often not achieved in turntable bearings. We go to great lengths to achieve optimum running conditions in your TD124 bearing.
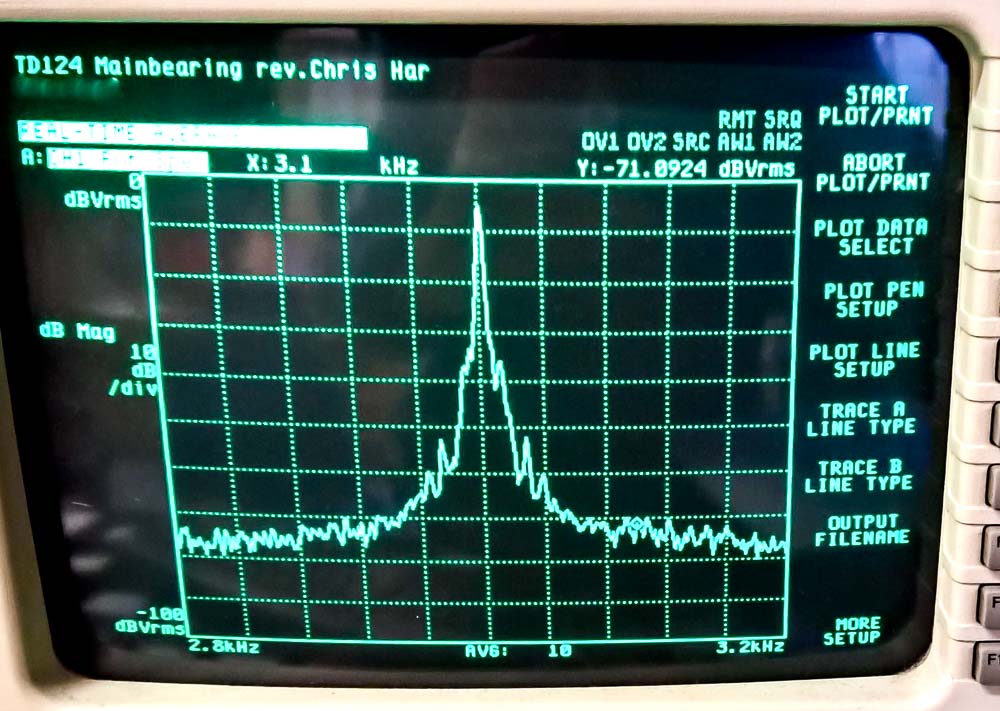
It is very likely that the bearing in your TD124 needs to be serviced. If your bearing has the original plastic bushings which were installed in some earlier TD124’s for a short period of time, these definitely need to be replaced, as the way that the bearing plastic that Thorens used created a long term unstable result. Thorens quickly stopped using the plastic bearing liners for a reason. If you can feel excessive ‘play’ in your main bearing, it needs to be serviced. If your spin down time is only around 1 minute, or less, it needs to be serviced. If you can see very noticeable wear marks on the spindle, it needs to be serviced. Our turnaround time is approximately 2 weeks. You will notice a significant improvement in your bearing function with our rebuild service.
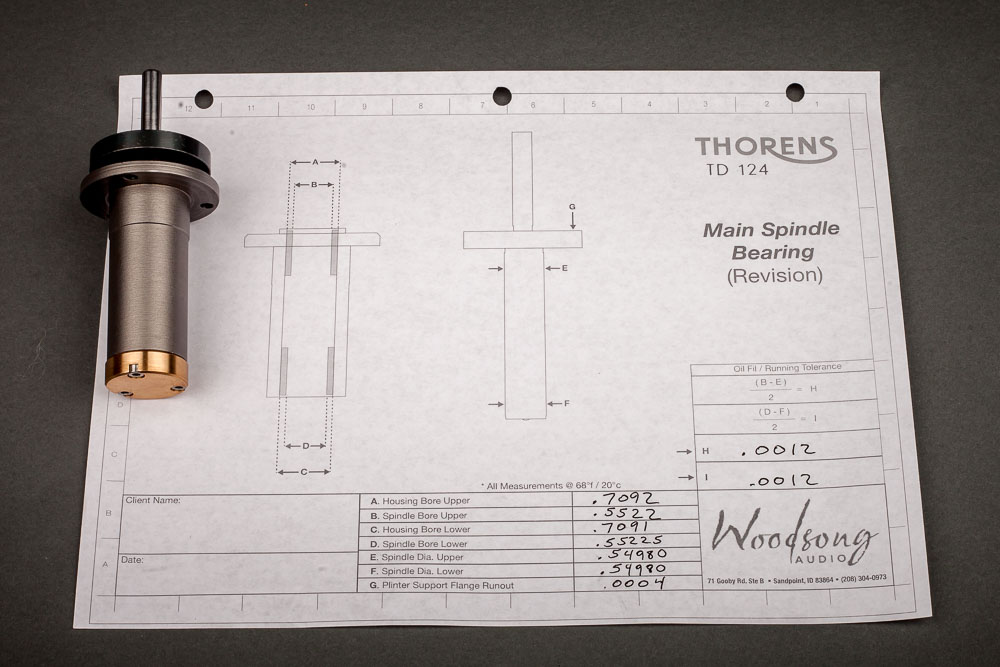
With our specialized TD124 bearing rebuild you can expect a ‘blueprinted’ close tolerance spindle fit, and a spin down time from 33rpm of over 2 minutes. Your bearing will be returned very noticeably better, and with a printout of the newly measured specs, as well as our excellent thrust bearing installed, and, your bearing will be leak-free.
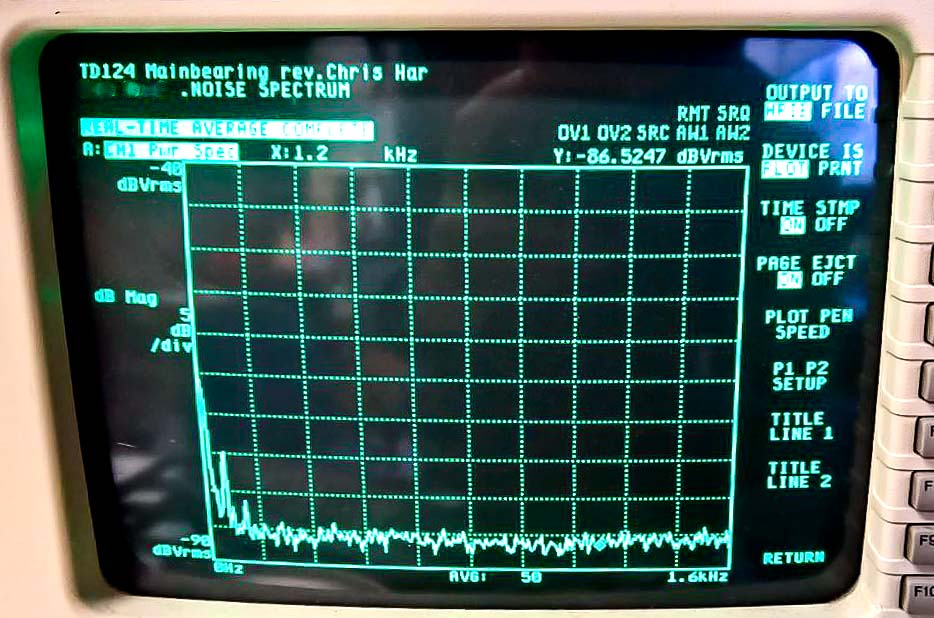
On receiving your bearing, we begin with a close examination of the main bearing assembly, looking for evidence of it’s current condition, and it’s likely history. We record the spindle diameter at each bushing location, and the bore i.d of both the upper and lower bushings. If, on the odd chance that we feel that your bearing does not need service, we will tell you. We have not seen a bearing, yet, that we have not improved greatly.
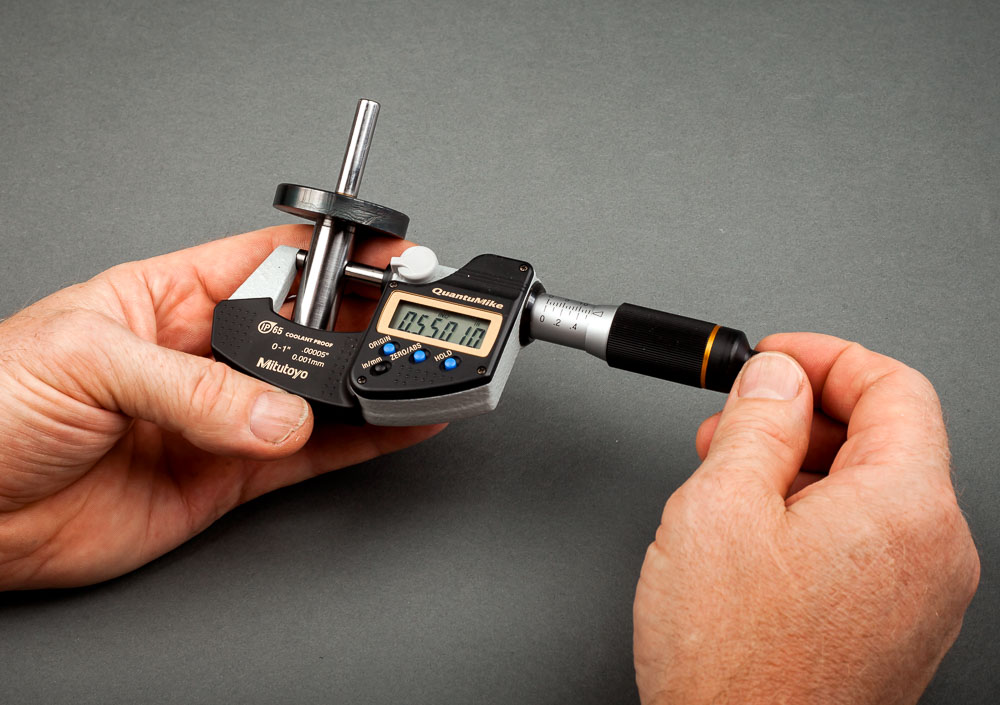
The old bushings are pressed out, and the bearing housing is fine glass bead blasted to restore the finish to new condition, and it is then ultrasonically cleaned to remove any debris. We measure the housing bore i.d. at the upper and lower bushing locations, and record them. We have seen the range of housing bore i.d.’s vary by almost 0.002″”, which is why we do this, and is also why we believe that a ‘one size fits all’ approach to servicing TD124 bearings is not optimal. One standard size bushing will not fit all housings very well, and in many cases, may not work at at all. If a bushing with a fixed o.d. dimension is pressed into housings which vary in i.d. the installed i.d. the bushings will vary corresponding with the i.d. of the housing bore, plus any variation in the bushing itself. In order to have control of the installed bushing bore i.d., bushings with different sized outer diameters must be on hand.
We manufacture precision sintered bronze bushings in different outer diameters insteps of 0.0002” (0.005mm) so that we can individually select bushings to fit each individual housing, precisely how we like.
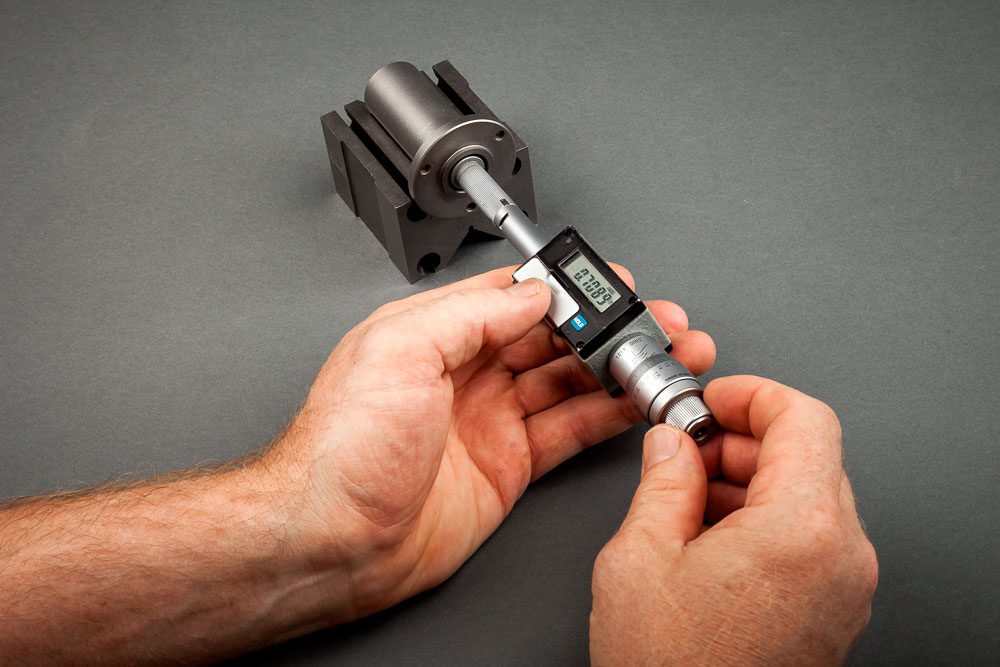
The brass clip holding the old steel thrust ball is carefully removed from the end of the spindle, and the ball is removed. The spindle is diamond polished, measured at the upper and lower bushing locations, and the measurements are recorded.
Bushings are fitted into the housing with what is known as a ‘press fit’, meaning that the new bushing o.d. is very slightly larger than the housing bore i.d. This is what holds the bushing in place. As an example, if the housing bore is _______, and the bushing o.d. is__________, _______ is the amount that the bushing is ‘oversized’ and is referred to a ‘interference. The i.d of the pressed bushing is reduced proportionately with the exact amount of ‘interference’.
We use highly precise and calibrated measuring tools for all measurements.
By calculating the measurements, we are able to precisely and consistently set the ‘running tolerance’ or oil ‘film gap’ of your bearing, giving consistent and excellent results that are clearly measurable, and directly audible. The original thrust bearing assembly on the TD124 is a thin metal cap and a 1mm thick plastic disc which always deforms to the steel thrust ball, and almost always has a large wear mark. The original thin aluminum cap is notorious for leaking out all of the oil.
With every bearing service, we also include a vial of the specialized oil which we use in our TD124 work. 10 drops of oil should be added every time the spindle is removed from the housing to replace oil which comes out with the spindle on removal. We use the modern equivalent of the same lubricant that was engineered for the TD124 bearing when it was originally manufactured.
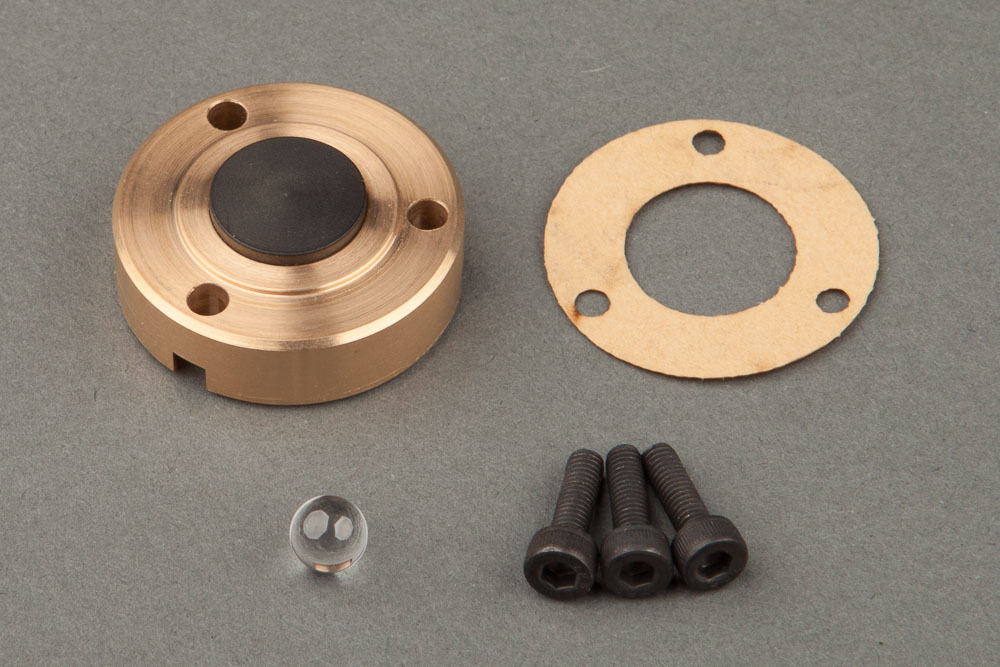
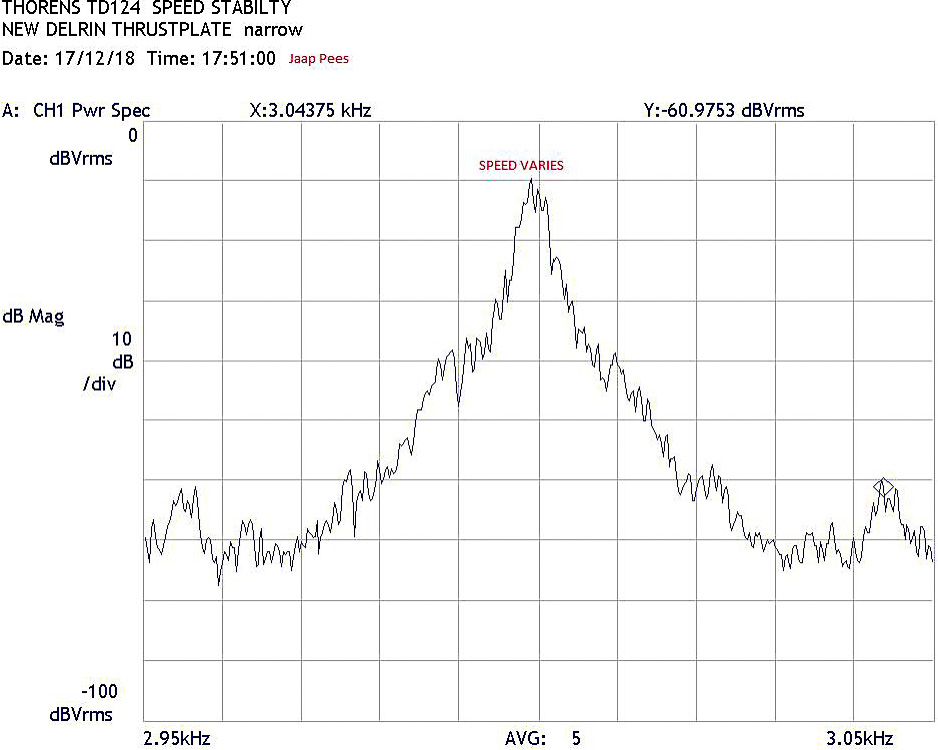
Photo provided by Jaap Pees of Hanze HiFi
In our rebuild process, we install our own thrust bearing assembly which consists of a 7mm thick bronze ‘cap’ which has a 5mm thick Torlon thrust surface recessed into it. We replace the original steel ball, with a much smoother, rounder, and harder Grade 5 sapphire thrust ball. This gives a longer lasting, and vastly superior thrust bearing to any other thrust bearing we have seen for the Thorens TD124. In addition, our thrust bearing cap will fit through the bearing well hole in the TD124 chassis, meaning that the entire main bearing assembly can be easily installed and removed from the chassis while the bearing cap is installed. With many of the other 124 thrust bearing designs, the thrust cap must be removed from the housing for installation or removal into the chassis, which is messy and very inconvenient. Our thrust bearing design will reduce drag, increase speed stability and improve spin down times, and it will maintain this over a much longer lifetime.
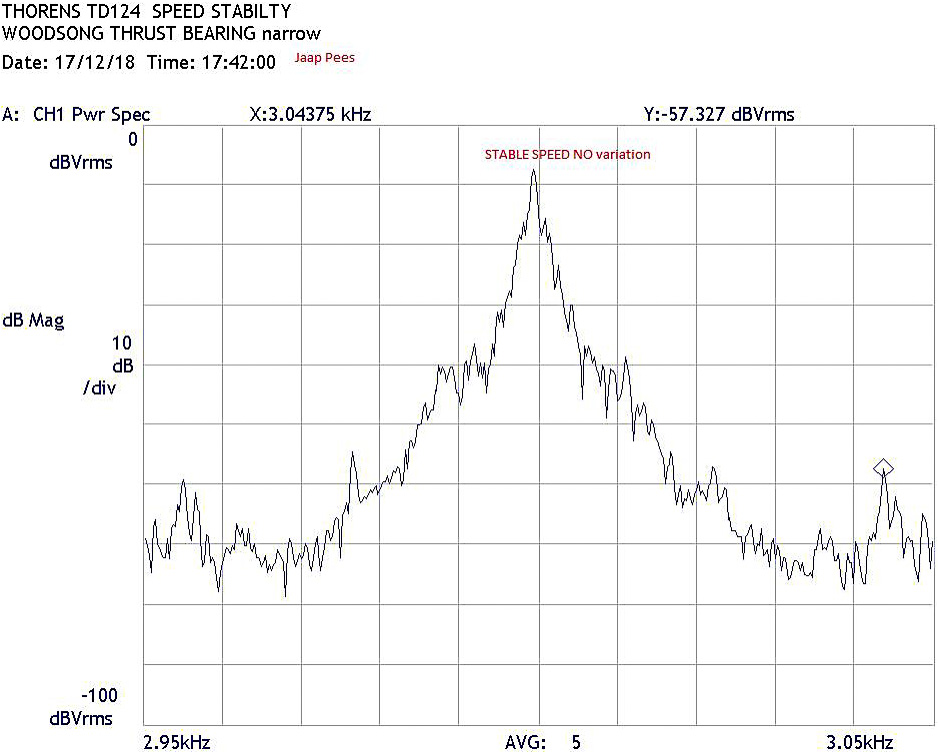
Photo provided by Jaap Pees of Hanze HiFi
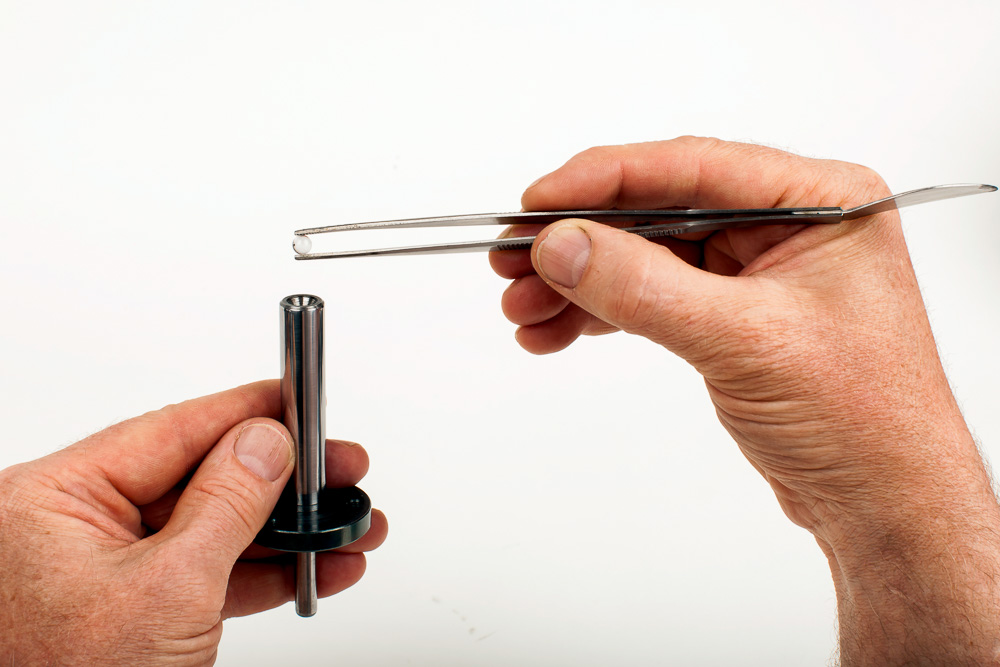
Our sintered bushings are impregnated with a high-quality lubricant which will not harden over time, and which has no additives which can contaminate the micro-porous structure of the bushings as well as react badly with the bronze itself. We recommend to never use oils which are intended for use in combustion engines, for your TD124 bearing.
After re-assembly, we install your bearing into a deck, and run it in. During this time, it is closely observed for correct operation, hydrodynamic running, and spin down time. If we see that anything is not correct, we take appropriate action after identifying the issue, such as installing a different bushing when necessary. The lubricant is changed numerous times in this period. Most of the time spent in servicing your bearing, is during this observation period, and we feel that it is by far the most important part of the service. This is far from a ‘remove and replace’, ‘in and out’ service. We take the time to ensure superior and consistent results, every time, which will help to ensure the highest performance from your TD124. When we are happy with your bearing, we give a final 14um micro cross hatch finish polish to the bearing spindle. Then we contact you, pack it up, and return your completed bearing.
“Concentricsized Bushings”
Sintered bronze bushings are made by pressing particles of bronze under extreme pressure and heat into a mold, creating a micro-porous structure that holds lubricant through capillary action in order to help maintain safe operation under compromised lubrication conditions,such as when the thin aluminum cap which is stock on all TD124 bearings, causes all of the oil to leak out, which happens in almost all TD124 bearings which have the original thrust bearing assembly.
One of the trademarks of our bearing work with TD124 bearings, is in our bushings and what we call ‘Concentricsized’ bushings. The ‘tolerances’ of manufactured bushings varies by manufacturer, but none are perfect. ‘Concentricity’ is one of the important tolerances in these bushings, and it refers to how perfectly the axis of each the outer diameter of the bushing, and the inner diameter of the bushing are aligned. This tolerance is often nowhere near as good as is ideal for a close tolerance turntable bearing. The tolerances in the TD124 bearing are critical to overall performance, and when the upper and lower bushings are not in alignment, which is very often the case based on what we have seen, even in bearings which were supposedly ‘professionally serviced’, the spindle will rub on the bushings causing metal to metal contact, poor speed stability, higher Wow measurements, higher noise, and sub-par audio playback quality, and which is detrimental to the longevity of your bearing spindle. Misalignment between the bushings means that the spindle cannot glide on a thin film of oil as it was intended, but instead, it ‘scrapes’ metal to metal.
We start with high quality, oversized sintered bronze bushings, and by mounting them onto a specialized tool in a CNC lathe that holds the bushing by the inner bore, precisely referencing off of the true axis of the bushing bore, we machine bushings with extreme concentricity between the inner bore,and the outer diameter. We never machine any ‘working’ bearing surfaces in sintered bronze, as we feel that any machining ‘smears’ the micro-porous oil holding structure, thus reducing the effectiveness of the sintered bronze. Machining the o.d. of the sintered bushings has no effect on the oil handling qualities of the bearing surface of the bushings.
The dimensions of the stock TD124 bushings are an i.d of about 14mm, an o.d. of about 18mm, and about 18mm tall. We have seen others use bushings which are 12mm tall in order to ‘work around’ this issue of misaligned bushings, and even then still end up with poor results. This is not a good solution in our view. The bushings that we use are of the same dimensions that were used by Thorens at the time of original manufacture.
We do not believe in the need for any ‘aftermarket’ bearing for the TD124. The original housing and spindle are of excellent quality, and are plenty good for a basis on which to build a great turntable bearing. What makes a good turntable bearing is not a shiny stainless housing or fancy materials. Precise control and execution of critical tolerances, and engineered selection of materials and lubricants are what make a great turntable bearing. When it is right, you can expect audibly superior performance, and excellent longevity.